In today’s manufacturing landscape, industrial filtration systems have become indispensable tools for businesses across various industries. They are critical for maintaining product quality and ensuring regulatory compliance. Filtration systems have also become environmental champions, helping minimize harmful emissions and waste products during the manufacturing process. The success and reputation of manufacturing operations hinge on several factors, including industrial filtration, which plays a critical role. This article digs into the reasons why industrial filtration systems are of the utmost importance to the manufacturing sector.
Protect Critical Equipment From Harmful Contaminants
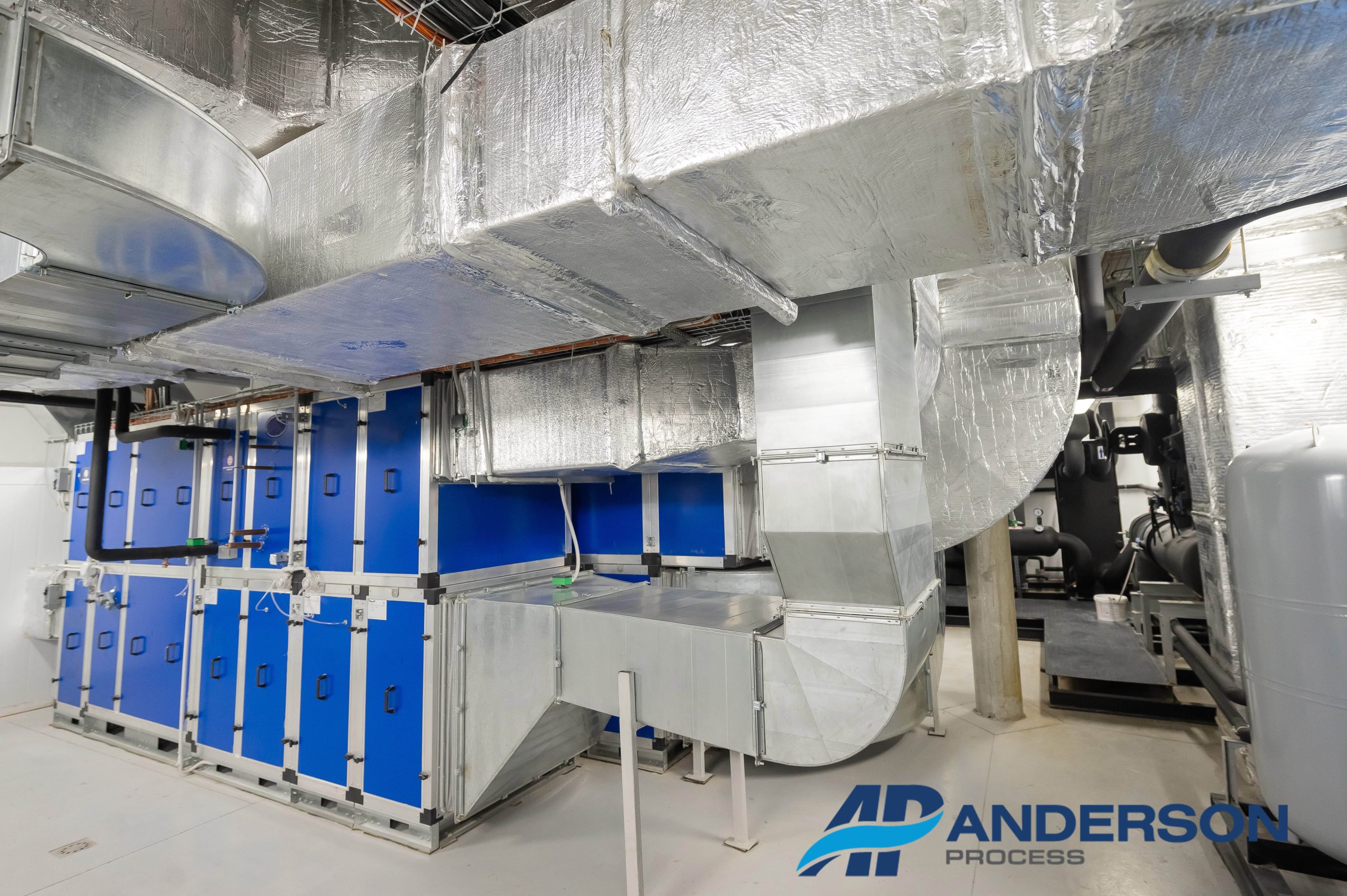
Industrial filtration protects systems from harmful contaminants that are present during the manufacturing process. They are responsible for capturing and removing contaminants, so they can be properly disposed of. In HVAC systems, for example, filters prevent particles from clogging sensitive components. This prevention aids in reducing maintenance requirements and contributes to extending the system’s lifespan. Industrial filtration is not only critical to protecting equipment but the surrounding environment as well. For instance, industrial air filtration systems are used to remove harmful byproducts of the manufacturing process, such as vapors and aerosols. These vapors and aerosols are dangerous and can lead to vacuum pump failure or potentially pose an explosive threat.
Photo: Industrial Air Filtration and Ventilation System
Decreases Production Costs
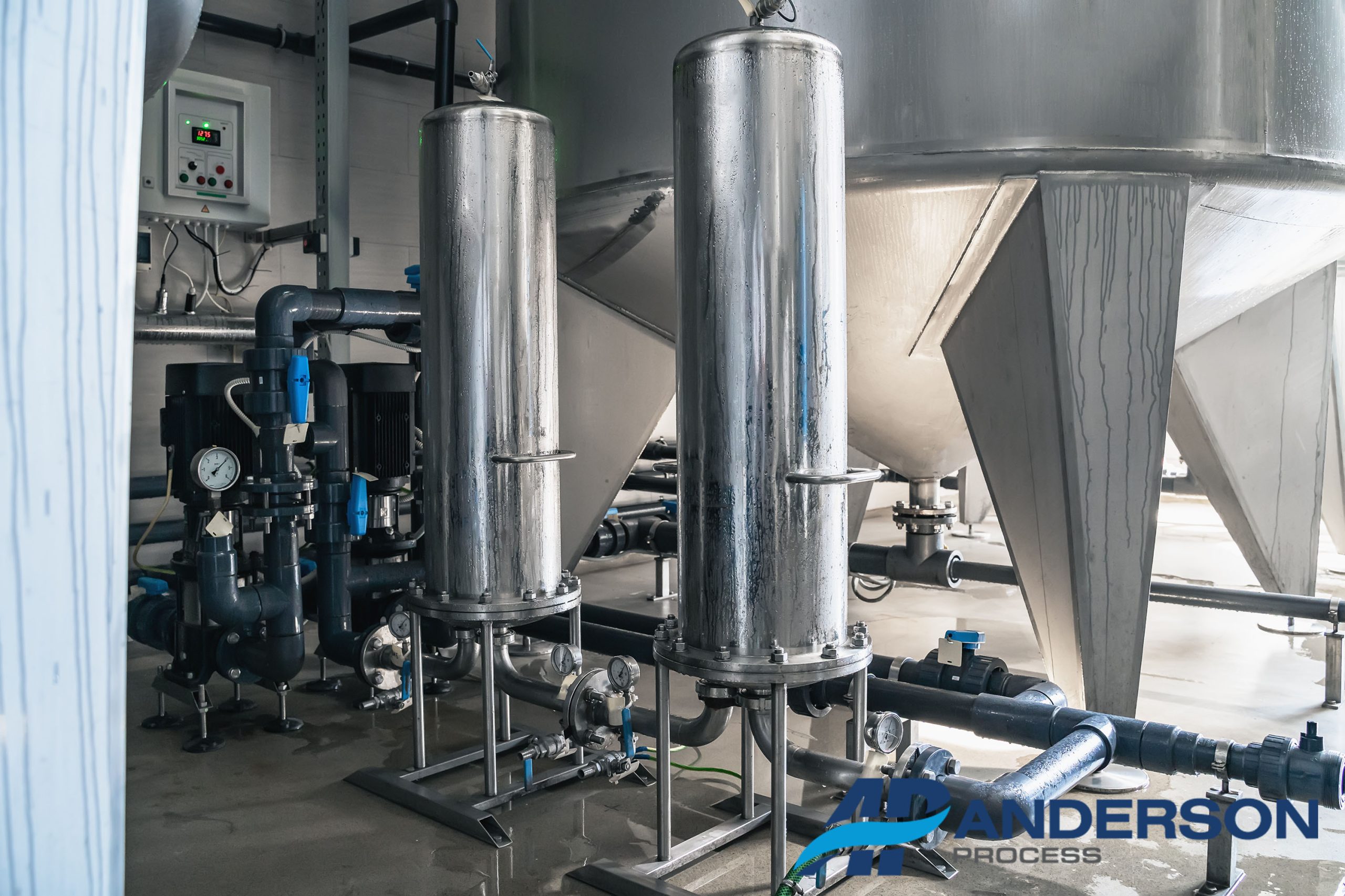
Contaminated, dirty machines expend more energy to get the job done than clean ones. Energy is wasted and unnecessary dollars are spent. Filtration systems prevent contaminants from entering sensitive equipment, such as pumps, valves, or process machinery. Removing debris, particles, or corrosive substances from fluids or gases reduces wear and tear on equipment, thus extending its lifespan. Instances of frequent repairs, maintenance, and equipment replacement are significantly reduced resulting in strong economic savings. Filtration improves process efficiency by providing clean fluids (lubricating oils, hydraulic fluids, cooling water, etc.) that minimize friction and reduce pressure drops. The result is improved production rates, yield, and reduced downtime. These factors all contribute to beneficial economic savings. Filtration technology enables the recovery of valuable resources from process streams or waste materials. By separating and removing solids, liquids, or contaminants manufacturers minimize waste generation and cut down on disposal costs. In most cases, the recovered materials can be reused or sold, generating potential revenue streams and lowering production costs. Filtration improves product quality and enhances overall efficiency. Going a step further, using self-cleaning filters or automated filter media replacement systems are great ways to reduce labor costs and improve operational efficiency. Cleanliness and efficiency are primary contributors to economic savings and filtration technology is terrific catalyst for those contributors.
Improved Product Quality
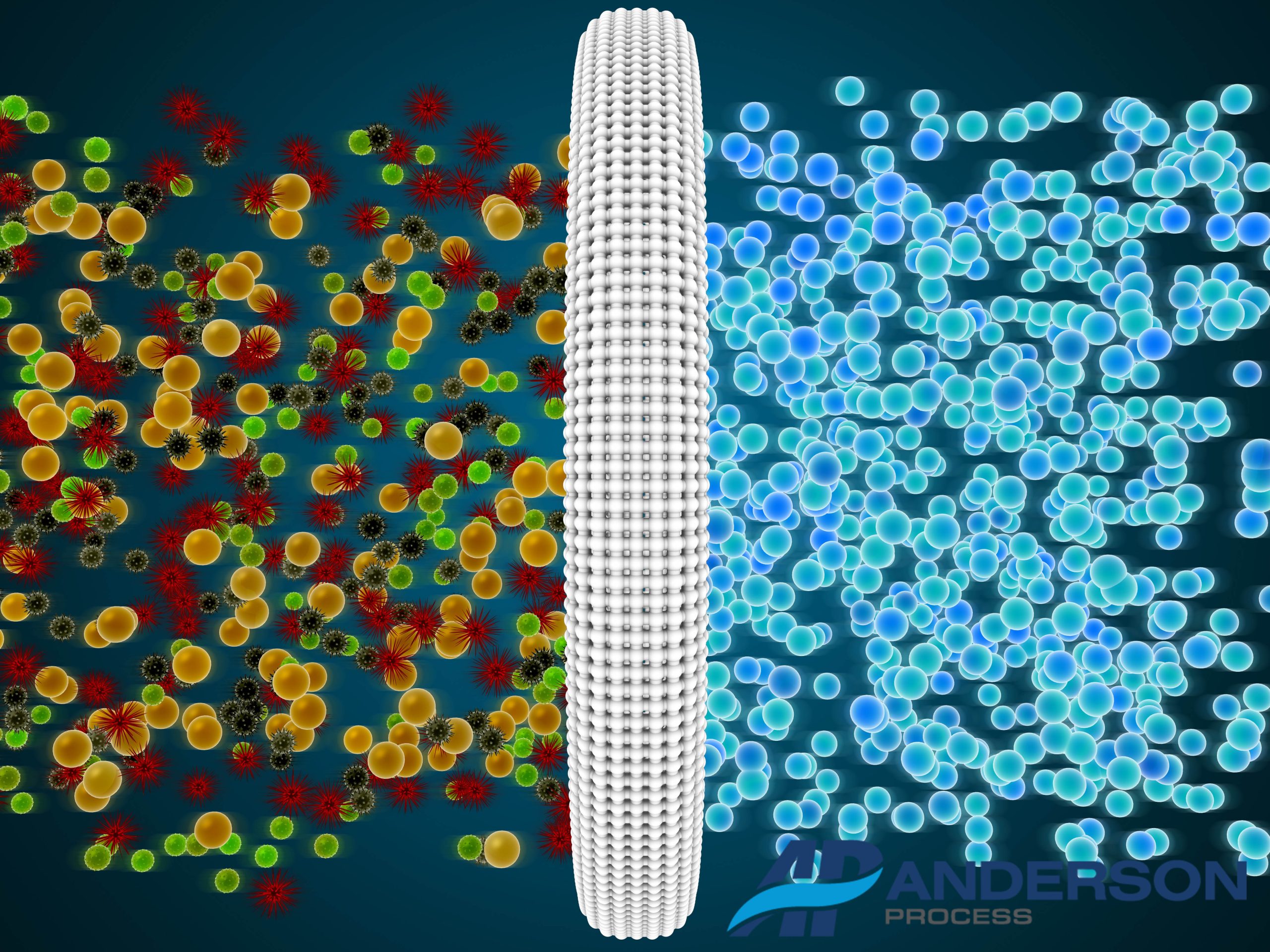
Accumulation of contaminants, such as dust, mold, extra moisture, and particles is an undesirable part of the manufacturing environment that can affect product quality. This makes maintaining a clean and controlled environment critically important. Filtration ensures that final products are of high quality, free from impurities, and meet required specifications. This is especially important in industries like pharmaceuticals, food processing, and electronics where product quality can’t afford to be subpar. Filtration helps protect equipment from paint overspray particulates in the air, usually from solid or liquid aerosols. They also help prevent waste, disposal, or possible recall due to a contaminated product batch.
Healthy and Safe Work Environments for Employees
Poor air quality reduces quality of life and increases the rates of respiratory infections, heart disease, stroke, and lung cancer. Air filtration systems contribute to a healthier and safer work environment for employees. Removing airborne contaminants such as dust, fumes, and hazardous chemicals helps prevent respiratory issues and occupational illnesses among workers. Workers are less sick, absent, and more productive as a result. In fact, several studies have reported that the quality of air affects employees’ overall well-being and as a result their productivity level. This leads to the conclusion that installing industrial filtration systems is not only important for equipment protection but for employees’ overall health as well.
Compliance with Environmental Regulations
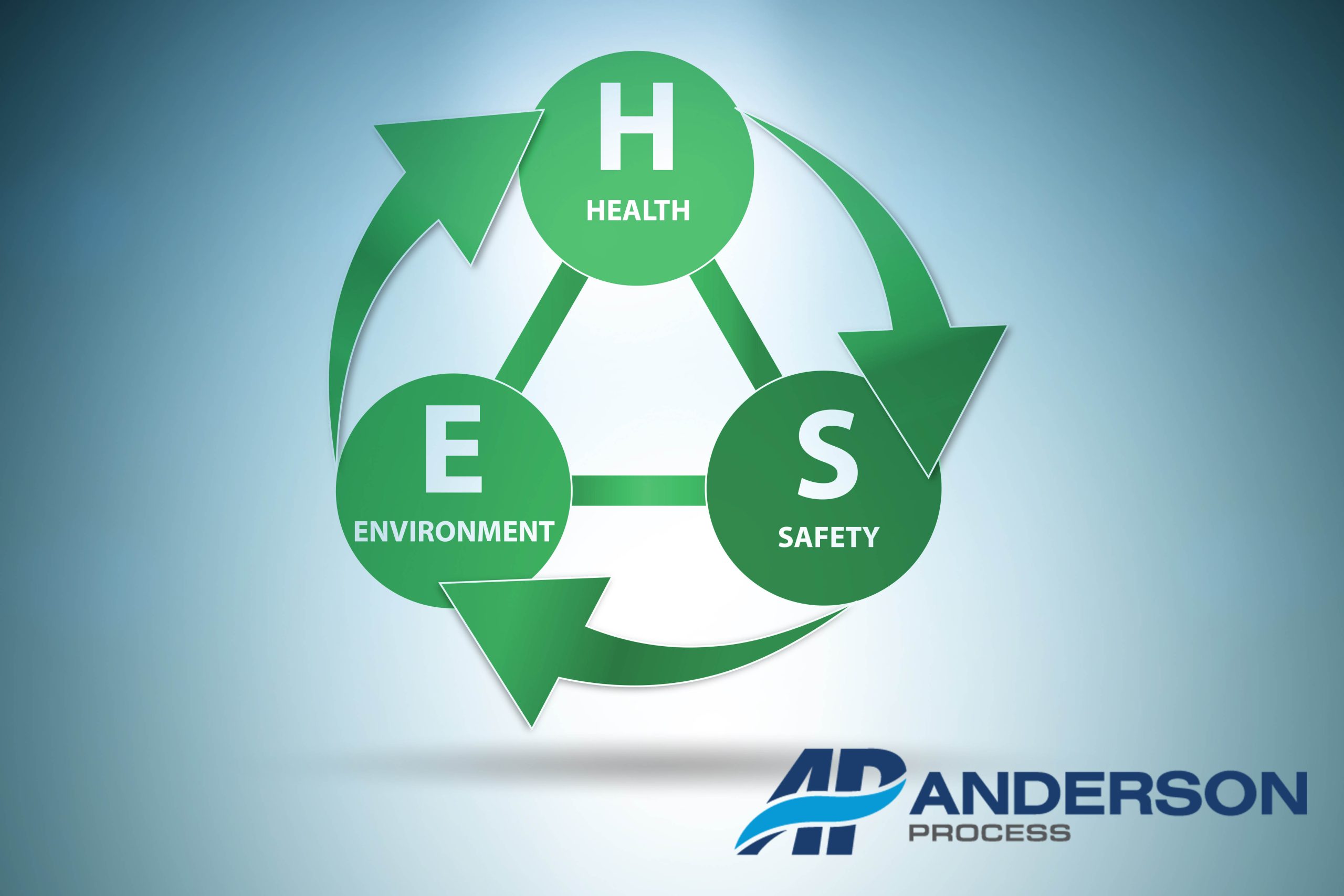
A crackdown on environmental emissions and waste management has affected many industries that must comply or face potentially expensive fines or worse. Industrial filtration aids in meeting environmental regulations by trapping and controlling airborne pollutants, volatile organic compounds (VOCs), and other harmful substances generated during the manufacturing process. Implementing an effective filtration system will help manufacturers lessen their environmental impact and ensure regulatory compliance. Filtration systems also contribute to energy efficiency, which indirectly helps manufacturers meet regulations. If a manufacturer has a smart and efficient filtration system in place, energy consumption from their process will be reduced and greenhouse gas emissions will be minimized.
Increased Energy Efficiency
A dirty machine is an inefficient and often costly machine. Clean air filtration systems help improve energy efficiency in manufacturing processes. Particulate matter and pollutants in the air are removed by air filters minimizing the buildup of residue on the equipment surface, reducing friction, and improving airflow. As a result, less energy is consumed, and machines operate more smoothly and don’t need as much power to run effectively. Filtration often plays a vital role in process optimization and ensuring the quality and cleanliness of fluids used in various manufacturing processes. Clean fluids have less friction due to controlled particle levels, so they run through pumps, pipelines, and valves with less energy loss than dirty fluids. Maintaining fluid cleanliness through filtration allows manufacturers to minimize energy consumption with pumping, fluid circulation, and other fluid-dependent processes.
Filtration Aids in Creating a Positive Public Perception
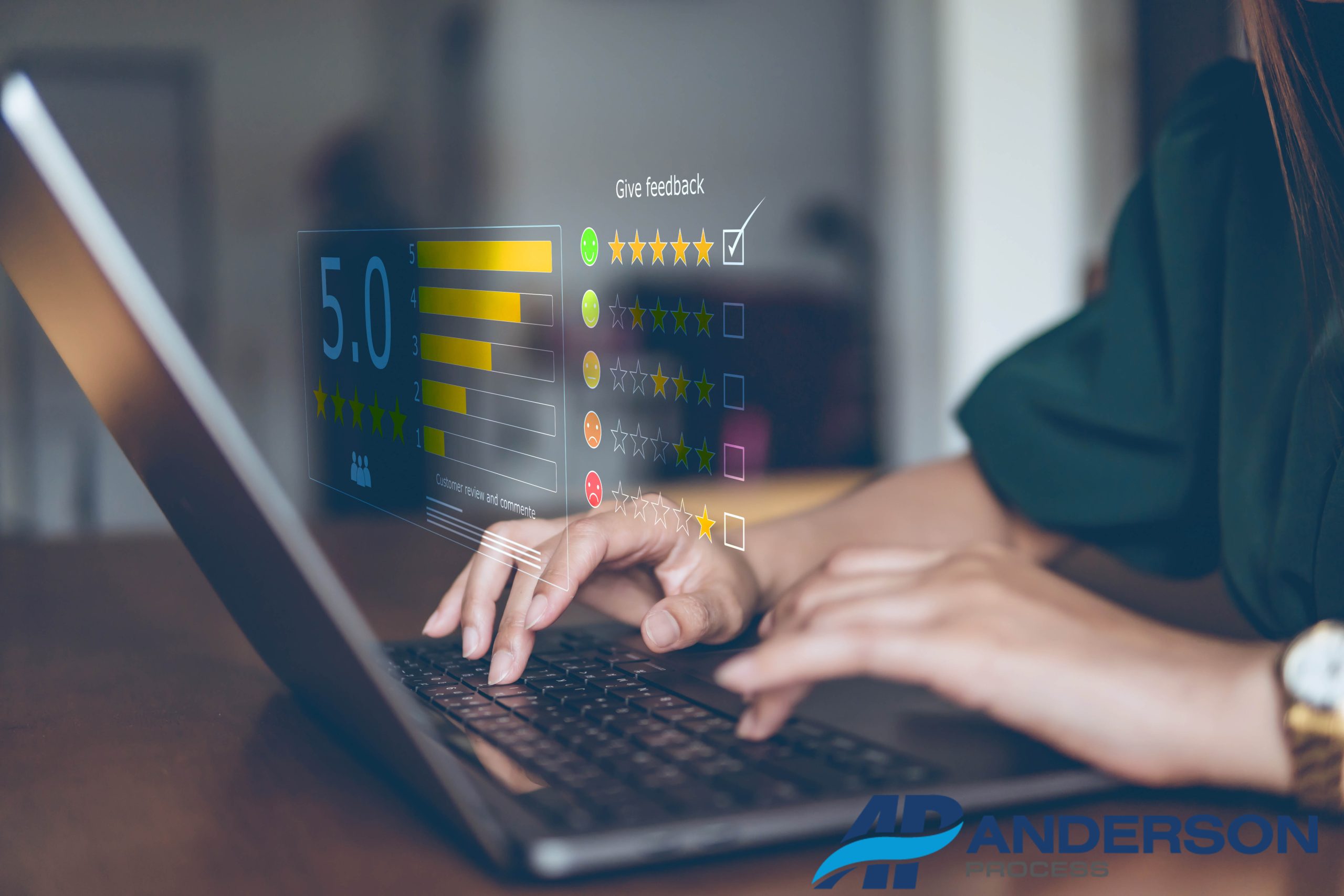
A manufacturer that prioritizes a clean and safe operation is more likely to gain a positive public perception than one who isn’t. When customers, communities, and investors perceive a company as environmentally conscious, committed to quality, and compliant with regulations it enhances the overall brand image. Positive public perception encourages customer loyalty, positive word of mouth recommendations and helps foster a competitive advantage in the market. Having a competitive advantage is especially true in industries where filtration is not mandated. A manufacturer utilizing filtration in a non-mandated industry will stand out with significantly improved product quality and one that prioritizes employee safety. The company will also likely be perceived as going above and beyond standard practices to deliver exceptional products and services.
Industrial filtration systems are vital components of modern manufacturing operations. They are important in ensuring product quality, establishing regulatory compliance, equipment protection, energy efficiency, waste reduction, and environmental sustainability. Investing in filtration technology aids manufacturers in optimizing their processes, reducing their costs, and enhancing brand reputation. As manufacturing continues to evolve, the importance of industrial filtration systems will only continue to grow making them indispensable tools for manufacturers.
Anderson Process is a key distributor for several filtration and filter technology manufacturers, including Filter Technologies, Inc. (FTI), Hy-Pro, Eaton, Global Filter, Glassfloss and Solberg.