In many industrial sectors, vacuum pumps are doing yeoman’s work. Often running for several hours per day in some applications and even non-stop for multiple work shifts per day. Vacuum pumps being in operation means several maintenance related issues inevitably will crop up. If the user is not proactive in treating these issues the vacuum pump will lose efficiency over time and/or potentially breakdown. Here are some tips to help extend the life of your vacuum pump.
Have a Regular Maintenance Plan
Stay organized by keeping a checklist of maintenance activities and a log of all activity (routine maintenance, component replacement, repairs etc…). Having a maintenance log is crucial in knowing what spare parts to stock, being able to adapt a regular maintenance plan (if needed) and diagnosing potential future problems. It’s good practice to install a running meter to document how many hours the pump is running while in service and entering it into the maintenance log. It also maybe a good idea (if possible) to electronically record the vacuum before and after each operating cycle as well as the ultimate vacuum level achieved. This data may help diagnose current and future issues.
Perform Regular Visual Inspections
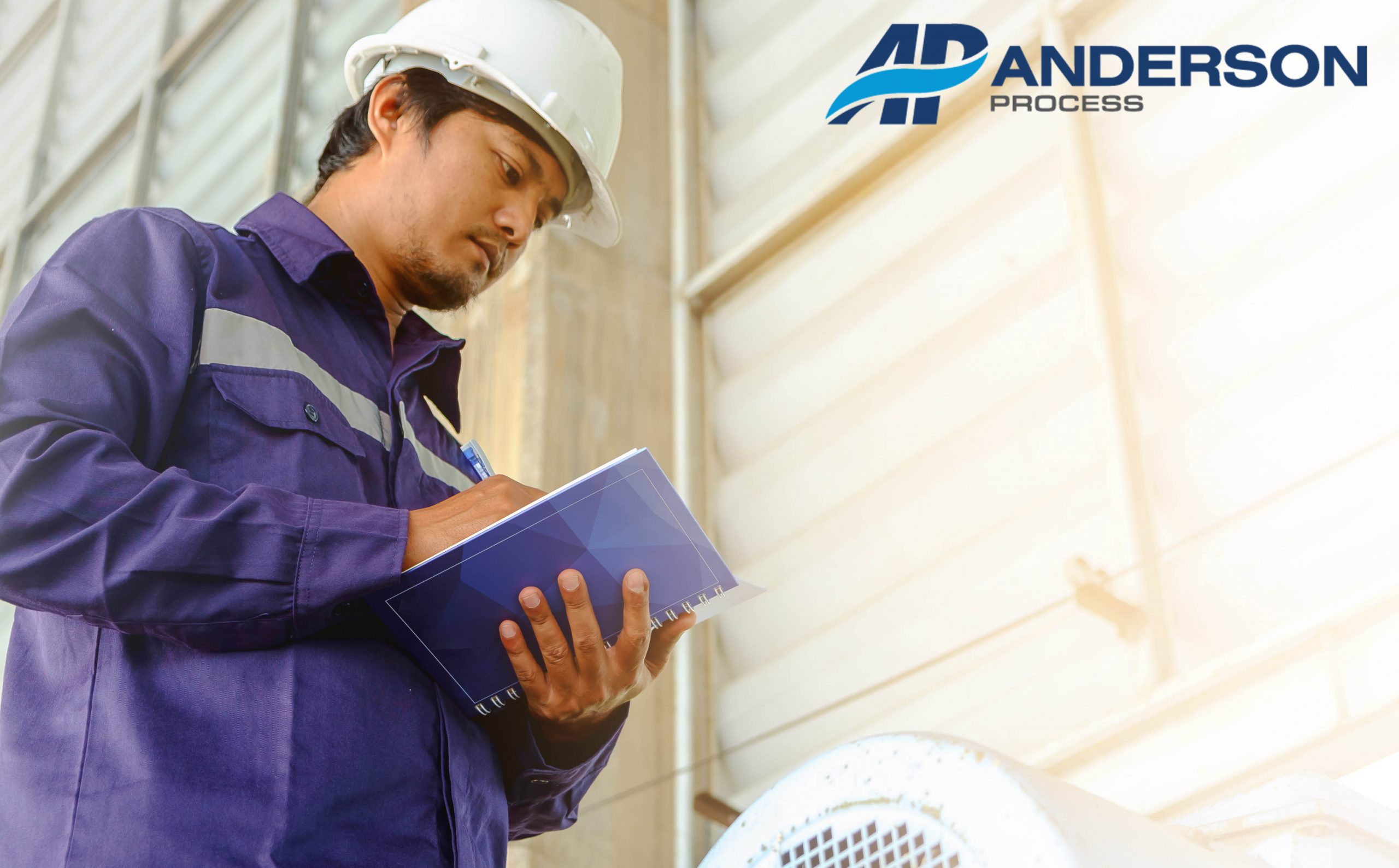
Since most vacuum pumps come with a sight glass, knowing what the oil level is for your pump is easy to recognize. Clean oil will look similar in color to Virgin olive oil, while oil that is contaminated will be on the darker side. Being able to visually recognize the color of the oil will help ensure oil changes are completed as needed. If the oil becomes too dark, the pump may be compromised and need servicing. Also, make sure the pump outlet is not blocked or obstructed in any way. If the pump outlet is blocked it could cause the pump to stop or the pressure buildup can loosen the seal around the oil sight-glass causing a leak that will need to be repaired. The visual inspection should not be limited to the pump itself, but the surrounding area as well. For example, oil or water in the pump’s general vicinity can possibly be the result of a leak. Unfamiliar sounds coming from the pump or efficiency related issues can also be the signs of a potential problem.
Examine the Surrounding Environment
For a vacuum pump to achieve peak performance, the right environmental conditions need to be in place. Clear air flow around the pump is critically important. Regularly checking the airflow and making sure there isn’t any changes that can affect the airflow around the pump is a good step. Are there any contaminants in the area, such as vapors, solvents, or acids that can cause alarm? If there are contaminants in the area, determine whether they could be affecting the pump’s performance. If their are corrosive vapors in the area that can’t be avoided, installing an inlet cold trap on the vacuum pump can help reduce the corrosive vapor load entering the pump. A liquid nitrogen cold trap is often a great choice for hazardous solvents. Changing weather can also be an issue. If the pump is near an outside wall or running heat into the building, condensation can build up and be cause for concern. Best practice is placing the pump in an ambient temperature environment if at all possible.
Regular Oil and Filter Changes are a Must
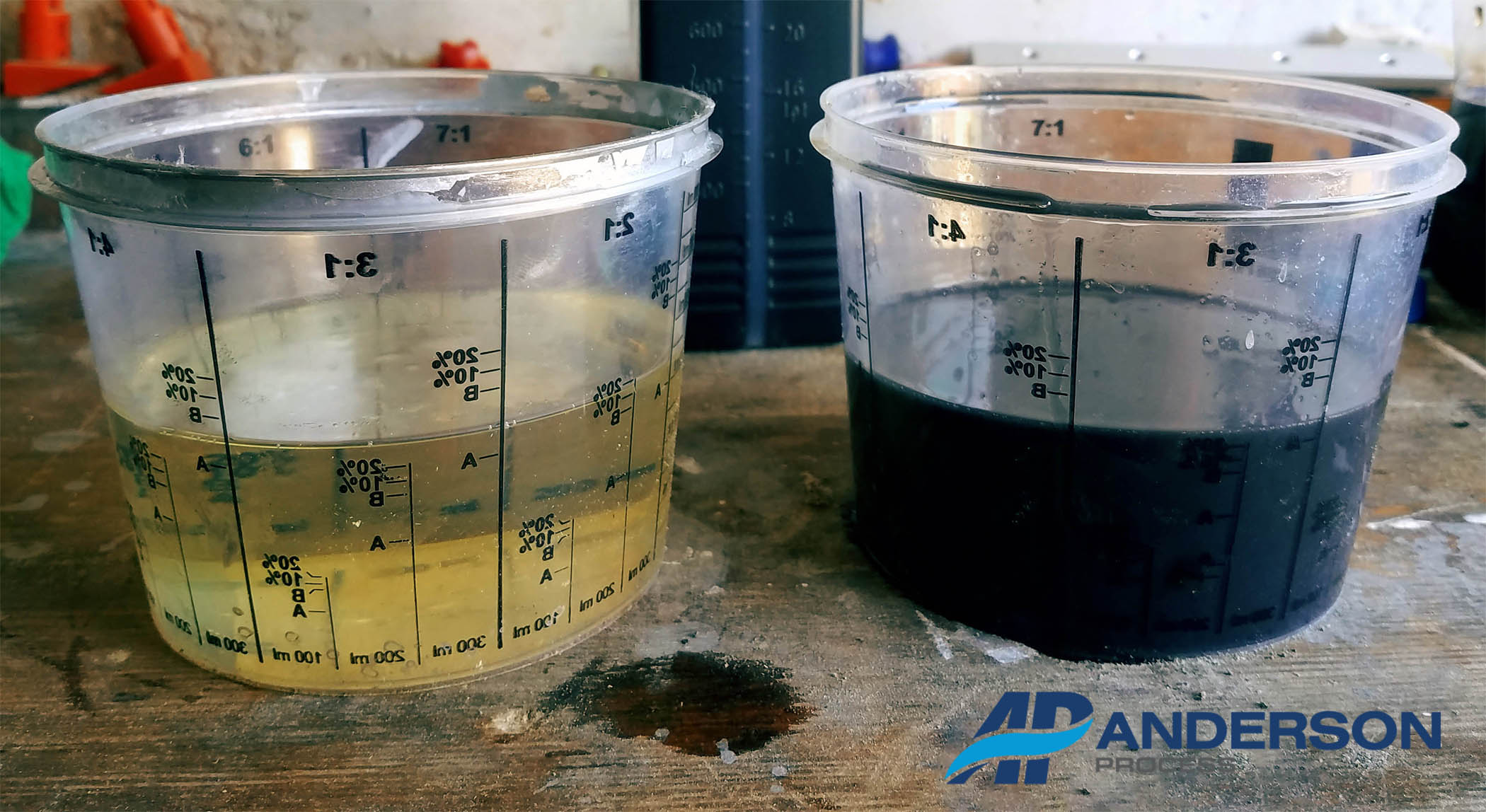
Over time, pump oil loses its lubricity by becoming oxidized or contaminated from vapors during the running process. Pump oil and filters need to be changed at regular intervals for the pump to achieve top performance and a healthy life. For wet pumps, such as rotary vane pumps, most manufacturers recommend the oil be changed every 3000 hours minimum. It is not unusual however, to change the oil monthly or weekly depending on how demanding the application is. Dry pumps usually require an oil change in the gearbox annually, but that is also subject to change depending primarily on pump usage. One way to extend the life of the pump’s oil is installing an inlet filter to help keep particulates out of the pump oil. The oil having a dark appearance without particulates, a cloudy, watery consistency indicating moisture in the system and the pump unable to reach its full vacuum are all indicators that the oil should be changed.
Regularly Complete Leak Tests
Completing regular leak tests after the vacuum pump is installed is essential to ensuring a vacuum tight seal through the various connections. Eliminating leaks can improve the pump’s lifespan and quality of its work. Keeping foreign elements, such as moisture, debris and oxygen away from the pump’s general environment is also necessary. These foreign elements can contaminate the pump, compromise its integrity, and reduce its overall effectiveness.
Incorporate Downtime into Your Maintenance Routine
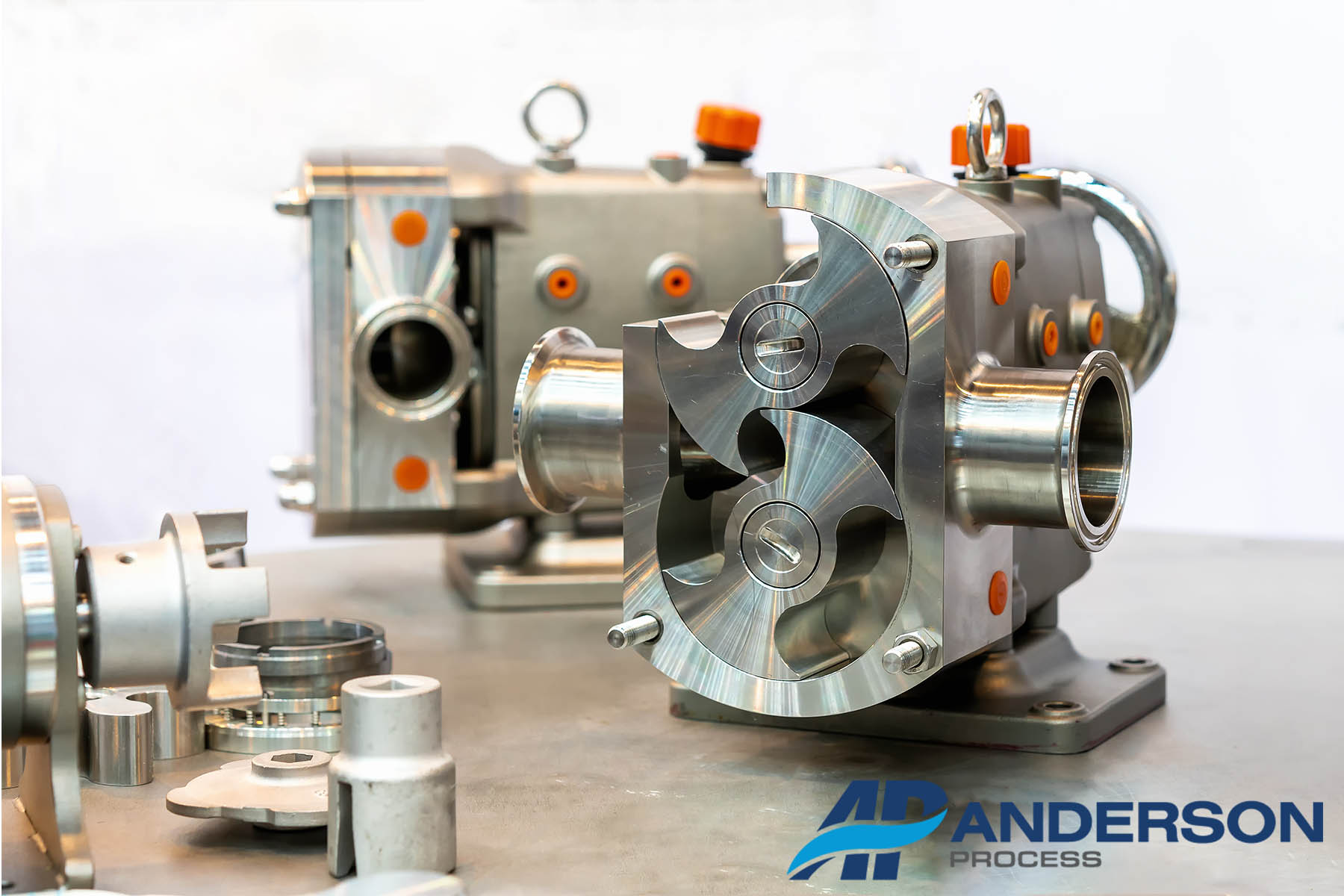
Every pump, including vacuum pumps, need downtime and maintenance to operate at top performance. It’s a good idea to have a spare pump on hand that can perform the same overall duties, while your vacuum pump is down for maintenance or is being serviced by a professional. Regular intervals where the pump is at rest is a staple for it continuing to operate at peak efficiency. It’s not a good idea to not have a backup plan for your pump. Being down without a pump can compromise your operation and leave it at a standstill.
In conclusion, the best ways to extend the life of your vacuum pump involve a regular maintenance routine and consistent visual inspections. Also, placing the pump in an environment that will not hamper its performance or enhance its risk for contamination. Following these tips will keep your vacuum pump in tip top shape for the years to come.