With over 60 years in the industry, we’ve seen many mismanaged pumps eat into the productivity and bottom line of businesses. Make sure you are getting the most out of your equipment by following these 10 ways to extend the life of your pump:
1. Regular Maintenance
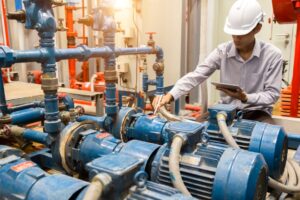
Before diving into specific aspects of pump maintenance, the most basic general rule of prolonging the life of your pump is to be proactive in cleaning and servicing the unit. The most common problems we see come through our repair facility are due to a lack of basic preventative maintenance. Bearing maintenance, proper lubrication, regular cleanings and proper operation will go a long way in extending the life of your pump. While it might be easier to run a pump to failure and send it in, it will end up costing you significantly more to repair or replace the unit.
2. Monitoring Shaft Wear
If you are properly maintaining your pump, then it is inevitable that the shaft and bearings will undergo cleanings and PM replacements. Replacing bearings and cleaning the shaft can actually wear down the shaft material over time. Eventually, it is possible that the shaft wear creates too much clearance between the bearing and the shaft, resulting in spinning bearings within the housing around the shaft.
It is also important to look for signs of a bent shaft. Operating outside of the BEP (Best Efficiency Point) of the pump can add additional pressure to internal components and even bend the shaft. A bent shaft can result in increased vibration and unwanted damage to other components.
3. Ensuring Proper Seals
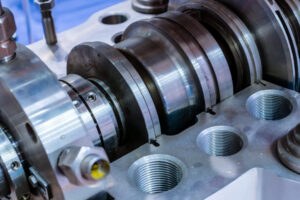
There are many seal options available to meet a wide variety of application needs. Choosing the correct seal for your application can be a tricky process. Using seals that don’t stand up to certain temperatures or chemicals can result in seal face damage, and eventually total pump failure.
Need help choosing the right seals? Our pump experts can help to ensure that you have the proper seals for every application.
4. Monitor Vibrations
One of the key indicators of problems within a pump is the vibration level during operation. Excessive vibrations can be the result of a variety of pump issues, including a bent shaft, imbalanced rotation components, misalignment, or misuse of the pump in its application.
Excessive vibrations will quickly ruin essential pump components like bearings, seal rings, bushings, and impellers, drastically shortening the life of the pump. In order to catch issues early, monitor pump vibrations to hone in on developing issues.
5. Ensure Proper Alignment
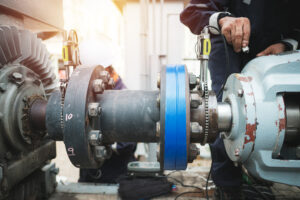
Misalignment is a leading cause of pump inefficiencies and failures. When shafts have angular or parallel misalignment, it takes more energy to operate at the proper specifications, increasing power consumption and making the pump less efficient. It can also lead to excessive vibration which can create problems with other crucial system components.
Anderson Process offers pump builds mounted on skids to ensure proper alignment through the shipping process and at the end-user facility. We also offer realignment services on-site and in our repair shop.
6. Monitor Lubrication Levels
As with any mechanical friction components, proper lubrication is essential to pump health and longevity. If the equipment is under-lubricated it runs the risk of bearings seizing prematurely. Too much lubricant can actually retain heat inside of the bearings and eventually cause oil leakages. Prevent premature failures by monitoring lubrication levels on a regular maintenance schedule.
7. Operate the pump at its BEP
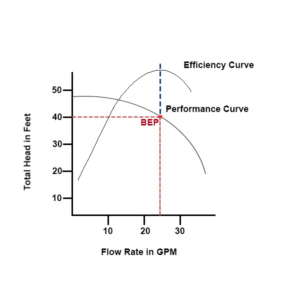
Pump curves and the BEP (Best Efficiency Point) provide information for the ideal operating parameters of every pump. Needless to say, operating at the manufacturer’s BEP will get the most out of your pump in terms of safety, productivity, and efficiency. While you might operate a pump within a tolerance of the BEP, going too far to the right of the performance curve will cause inefficiencies like excessive vibration, internal temperatures, and re-circulation.
Need help sizing a pump to an application? Contact our team to speak with a pump expert to guide you through the process.
8. Don’t Run the Pump Dry
Unless specifically designed to allow for dry run operations, running a pump dry is detrimental to internal components. When a pump runs with little to no fluid it is at risk for cavitation and overheating. The shaft and bearings can create heat without proper lubrication, leading to excessive wear and even melting of the plastic casing. Mechanical seals can be compromised or completely destroyed due to thermal shock.
As a general rule, always know your pump’s specifications and limitations before operating. Never dry run a standard pump. If you need dry-run options, we can help you find the pump to meet your requirements.
9. Know What You’re Pumping
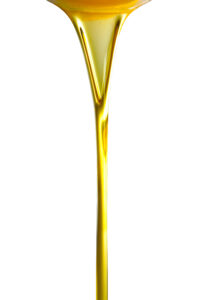
The vast range of available pump options can be partly contributed to the many different fluids that need to be handled. Food & Beverage fluids, wastewater, fuel, and harmful chemicals all require specific build materials to ensure product and operational integrity. Pumping the wrong medium, especially in chemical handling applications, can be detrimental to a pump’s internal components. The wrong chemical can cause corrode the components causing failure and spillage.
On the same note, pumping solids or abrasives in a pump designed for less viscous fluids can clog components and lead to premature failure. Be mindful of what your pump is capable of. When in doubt, consult the pump manufacturer or your solutions provider first.
10. Check the Piping Around Your Pump
If you’re doing all of the above and still experiencing issues with your pump, try taking a look at the surrounding piping system. Improper design or installation of piping systems can create pipe strain – unwanted pressure in the piping system – that leads to unwanted conditions within the pump itself. Be sure to check pipe supports, connections, bends, and areas of thermal changes that could be affecting the flow of fluid into the intake of the pump.